In today’s fast-paced business environment, the efficient and accurate allocation of costs is more critical than ever. What is the role of automation in cost allocation? It’s a question that delves into the core of modern financial management. Traditional methods, often cumbersome and prone to human error, are increasingly giving way to automated solutions that promise to revolutionize how businesses understand and manage their expenses.
This exploration will navigate the landscape of cost allocation, from its fundamental principles to the cutting-edge technologies driving its evolution. We’ll examine how automation streamlines data collection, enhances accuracy, and provides real-time insights, ultimately empowering organizations to make more informed decisions and optimize their financial performance. The journey will cover the various industries and tools available, providing a comprehensive view of this transformative process.
Introduction to Cost Allocation and Automation
Cost allocation is a fundamental practice in accounting and business management, playing a crucial role in determining the true cost of products, services, and activities. It involves assigning costs to specific cost objects, such as departments, products, or projects, based on a logical and systematic approach. This process provides valuable insights into profitability, pricing strategies, and operational efficiency. Automation is rapidly transforming various business processes, and its application to cost allocation offers significant advantages in terms of accuracy, efficiency, and strategic decision-making.
Fundamental Principles of Cost Allocation
Cost allocation adheres to several key principles that ensure fairness, accuracy, and relevance. These principles guide the assignment of costs to the appropriate cost objects, providing a reliable basis for financial reporting and management decisions.The core principles include:
- Cause and Effect: Costs should be allocated based on the cause of the cost. For example, the cost of electricity consumed by a machine should be allocated to the products manufactured by that machine.
- Benefits Received: Costs should be allocated to cost objects that benefit from the resources consumed. For example, the cost of marketing activities should be allocated to the products or services that are promoted.
- Fairness: Allocation methods should be equitable and avoid arbitrary assignments. This ensures that the cost objects are not unfairly burdened with costs.
- Materiality: Significant costs should be allocated with greater precision than immaterial costs. The level of detail in the allocation process should be proportionate to the importance of the cost.
- Consistency: Once a cost allocation method is chosen, it should be applied consistently over time to ensure comparability of financial results.
Traditional Cost Allocation Methods
Traditional cost allocation methods have been used for decades and offer a starting point for understanding how costs are assigned. However, these methods can be time-consuming and may not always reflect the complexities of modern business operations.Some of the commonly used methods include:
- Direct Labor Hours: Costs are allocated based on the number of direct labor hours used to produce a product or service. This method is relatively simple but may not be accurate in highly automated environments.
- Machine Hours: Costs are allocated based on the number of machine hours used. This method is suitable for production processes that are heavily reliant on machinery.
- Direct Materials Cost: Costs are allocated based on the cost of direct materials used. This method is simple but may not be appropriate for all cost objects.
- Percentage of Revenue: Costs, particularly overhead costs, are allocated based on a percentage of revenue. This method is simple but may not accurately reflect the resources consumed by each product or service.
- Activity-Based Costing (ABC): This method identifies activities as the basis for allocating costs. ABC is a more sophisticated approach that provides a more accurate allocation of costs, especially in complex business environments.
For instance, consider a manufacturing company using direct labor hours to allocate overhead costs. If the overhead costs are $100,000 and the total direct labor hours are 10,000, the overhead rate would be $10 per direct labor hour. If a product requires 2 direct labor hours, it would be allocated $20 in overhead costs. This approach, while simple, might not accurately reflect the actual consumption of resources by each product, especially if the production process is highly automated.
How Automation is Transforming Business Processes
Automation is rapidly transforming various business processes across industries. By leveraging technology, businesses can streamline operations, reduce costs, and improve efficiency.Automation’s impact can be seen in:
- Robotic Process Automation (RPA): RPA uses software robots to automate repetitive tasks, such as data entry, invoice processing, and report generation. This frees up human employees to focus on more strategic activities.
- Artificial Intelligence (AI) and Machine Learning (ML): AI and ML are used to automate complex decision-making processes, such as demand forecasting, inventory management, and fraud detection. These technologies can analyze large datasets and identify patterns that humans might miss.
- Cloud Computing: Cloud computing provides scalable and cost-effective infrastructure for businesses to store and process data. This allows businesses to access data and applications from anywhere and at any time.
- Enterprise Resource Planning (ERP) Systems: ERP systems integrate various business functions, such as finance, accounting, manufacturing, and human resources, into a single system. This improves data visibility and collaboration across departments.
- Data Analytics and Business Intelligence (BI): Data analytics and BI tools help businesses analyze data and generate insights. This enables businesses to make better decisions and improve performance.
For example, in a financial institution, RPA can automate the reconciliation of bank statements, a task previously performed manually. This reduces the time required for reconciliation, minimizes errors, and improves the efficiency of the finance department.
Potential Benefits of Automating Cost Allocation
Automating cost allocation offers numerous benefits, enhancing the accuracy, efficiency, and strategic value of this critical business process. The integration of technology allows for more precise and timely allocation of costs, leading to improved decision-making and better financial outcomes.The key benefits of automating cost allocation include:
- Increased Accuracy: Automation reduces the risk of human error, leading to more accurate cost allocations. This is particularly important in complex business environments where manual calculations can be prone to mistakes.
- Improved Efficiency: Automation streamlines the cost allocation process, saving time and resources. Tasks that previously took hours or days can be completed in minutes or seconds.
- Enhanced Timeliness: Automated systems can generate cost allocation reports in real-time, providing timely insights into costs and profitability. This allows businesses to respond quickly to changes in the market.
- Greater Transparency: Automated systems provide a clear audit trail, making it easier to track how costs are allocated. This increases transparency and accountability.
- Better Decision-Making: Accurate and timely cost information enables better decision-making related to pricing, product mix, and resource allocation. Businesses can make more informed decisions based on reliable data.
- Cost Savings: Automation can reduce labor costs and improve operational efficiency, leading to significant cost savings. The initial investment in automation can often be offset by long-term cost reductions.
- Scalability: Automated systems can easily scale to handle increasing volumes of data and transactions. This is particularly important for growing businesses.
Consider a retail company that uses automation to allocate marketing costs across different product lines. The automated system tracks marketing expenses and revenue generated by each product line. This data is then used to calculate the return on investment (ROI) for each product line, enabling the company to optimize its marketing spend and allocate resources to the most profitable products.
This level of detail and insight is often unattainable with manual cost allocation methods.
Automated Data Collection and Preparation
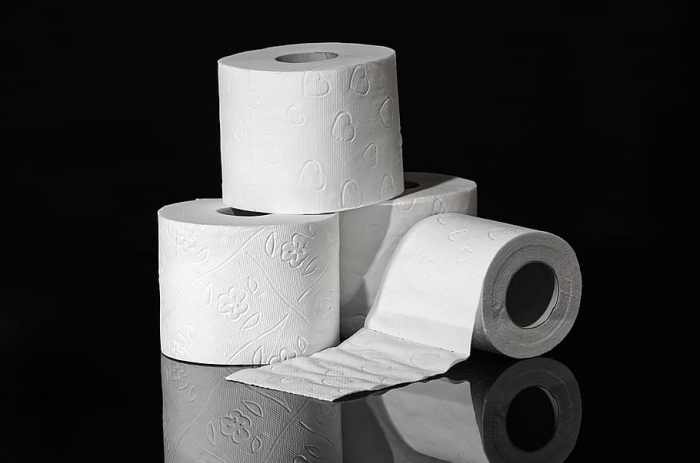
Automated data collection and preparation are crucial for effective cost allocation. They significantly reduce the time, effort, and potential for errors associated with manual processes. By streamlining these initial stages, automation lays the groundwork for more accurate and reliable cost allocation outcomes, leading to better decision-making.
Streamlining Data Gathering for Cost Allocation
Automated data collection simplifies the process of gathering information needed for cost allocation. Instead of manually collecting data from various sources, automated systems can pull data directly from source systems. This reduces the need for human intervention and minimizes the risk of transcription errors.
Comparison of Manual and Automated Data Preparation
Manual data preparation is labor-intensive and prone to errors. It involves manually gathering data from various sources, such as invoices, timesheets, and production records, and then entering it into spreadsheets or other systems. This process is time-consuming and susceptible to human error. Automated data preparation, on the other hand, uses software and technology to gather, clean, and transform data automatically.
- Manual Data Preparation: Involves manual data entry, which is time-consuming and prone to errors. It requires significant human resources and is often inefficient.
- Automated Data Preparation: Uses software to gather, clean, and transform data automatically, saving time and reducing errors. This process improves efficiency and allows for faster analysis.
Tools and Technologies for Automated Data Collection
Various tools and technologies facilitate automated data collection. These systems integrate with existing business systems, such as ERP (Enterprise Resource Planning) and CRM (Customer Relationship Management) systems, to extract relevant data.
- ERP Systems: ERP systems, like SAP and Oracle, provide a centralized database for financial and operational data, enabling automated data extraction.
- CRM Systems: CRM systems, such as Salesforce, capture customer-related data, which can be integrated into cost allocation processes.
- Data Integration Platforms: Tools like Informatica and Dell Boomi connect different data sources and automate the flow of data into cost allocation systems.
- APIs: Application Programming Interfaces (APIs) enable systems to communicate and exchange data automatically.
Data Validation and Cleansing Within Automated Systems
Automated systems incorporate data validation and cleansing processes to ensure data accuracy and reliability. These processes identify and correct errors, inconsistencies, and missing values, improving the quality of the data used for cost allocation.
Data validation and cleansing typically involve:
- Data Validation Rules: These rules check data against predefined criteria to identify errors, such as incorrect formats or out-of-range values. For example, a rule might ensure that a cost center code is a valid entry from a predefined list.
- Data Cleansing Techniques: These techniques correct identified errors and inconsistencies. This might involve removing duplicate entries, correcting typos, or imputing missing values based on statistical methods. For example, if a timesheet entry is missing, the system might estimate the time spent based on the employee’s average work hours.
- Data Transformation: This process converts data into a format suitable for analysis. For example, it might involve converting currency values to a common base or aggregating data at different levels of granularity.
Automation of Cost Allocation Methods
Automating cost allocation methods significantly enhances efficiency, accuracy, and the ability to make informed decisions. By leveraging technology, businesses can streamline processes, reduce manual effort, and gain deeper insights into their cost structures. This section explores the automation of key cost allocation techniques, including Activity-Based Costing (ABC), direct costing, and overhead allocation, demonstrating how these automations impact cost management.
Design a workflow for automating activity-based costing (ABC)
Automating Activity-Based Costing (ABC) involves a structured workflow that leverages software and data analytics to assign costs to activities and ultimately to products or services. This process reduces the manual effort traditionally associated with ABC, making it more practical and efficient.The workflow for automating ABC can be broken down into the following steps:
- Define Activities and Cost Objects: The initial step involves identifying the key activities performed within the organization and the cost objects (e.g., products, services, customers) to which costs will be assigned. For example, in a manufacturing company, activities might include machine setup, inspection, and order processing. Cost objects could be individual product lines.
- Identify Cost Drivers: Determine the cost drivers for each activity. Cost drivers are the factors that cause costs to be incurred. Examples include machine hours for machine setup, number of inspections, and number of orders processed.
- Collect Activity Data: Gather data related to the activities and cost drivers. This data collection can be automated through various means, such as:
- Enterprise Resource Planning (ERP) Systems: ERP systems often track data related to production, sales, and other operational activities.
- Manufacturing Execution Systems (MES): MES can provide real-time data on machine usage, labor hours, and other production-related activities.
- Customer Relationship Management (CRM) Systems: CRM systems can provide data on customer interactions, order processing, and sales activities.
- Calculate Activity Rates: Determine the cost per unit of each cost driver. This is done by dividing the total cost of each activity by the total activity volume. For example, if the total cost of machine setup is $10,000 and the total machine setup hours are 500, the activity rate is $20 per machine hour.
- Assign Costs to Cost Objects: Allocate costs to cost objects based on their consumption of activities. This is done by multiplying the activity rate by the amount of the cost driver consumed by each cost object. For example, if Product A requires 10 machine hours for setup, the setup cost allocated to Product A would be $200 (10 hours – $20/hour).
- Analyze and Report: Generate reports that show the cost of each cost object, broken down by activity. Analyze the results to identify areas for cost reduction and process improvement.
Organize the steps involved in automating direct costing
Automating direct costing, also known as variable costing, simplifies the process of assigning costs to products or services by focusing on variable costs. This method is particularly useful for short-term decision-making, as it provides a clear view of the impact of changes in production volume on profitability.The steps involved in automating direct costing include:
- Identify Variable Costs: Classify all costs as either variable or fixed. Variable costs change in proportion to the level of production or sales, while fixed costs remain constant within a relevant range. Examples of variable costs include direct materials, direct labor, and variable manufacturing overhead.
- Track Variable Costs: Implement systems to accurately track variable costs. This can involve integrating data from various sources, such as purchase orders, time sheets, and production reports.
- Calculate Cost per Unit: Determine the variable cost per unit for each product or service. This is done by dividing the total variable costs by the number of units produced or sold. For example, if the total variable costs for producing 1,000 units are $50,000, the variable cost per unit is $50.
- Prepare Contribution Margin Income Statement: Automate the preparation of the contribution margin income statement. This statement separates variable costs from fixed costs to show the contribution margin, which is the revenue remaining after deducting variable costs. The contribution margin helps in assessing the profitability of each product or service.
Contribution Margin = Sales Revenue – Variable Costs
- Analyze and Report: Generate reports that provide insights into profitability, break-even points, and the impact of changes in sales volume on profit. Use software to create dashboards and visualizations that highlight key performance indicators (KPIs).
Create examples of how automation impacts overhead allocation
Automation significantly impacts overhead allocation by improving accuracy, efficiency, and the ability to handle complex allocation methods. It reduces the manual effort required for overhead allocation, freeing up resources and enabling more timely and accurate cost information.Examples of how automation impacts overhead allocation include:
- Automated Data Collection: Automation streamlines the collection of overhead costs and activity data. For instance, software can automatically gather data from ERP systems, such as machine hours, labor hours, and utility consumption, which are then used as bases for overhead allocation.
- Real-time Allocation: Automated systems can allocate overhead costs in real-time or near real-time. This allows for more immediate insights into product or service costs, which is crucial for timely decision-making. For example, a manufacturing company can use automated systems to allocate overhead costs based on machine hours as soon as the data is recorded by the machines.
- Complex Allocation Methods: Automation supports the use of more sophisticated overhead allocation methods, such as ABC, which would be impractical to implement manually. ABC systems can allocate overhead costs to activities and then to products or services based on their consumption of activities.
- Improved Accuracy: Automated systems reduce the risk of human error in data entry and calculations, leading to more accurate overhead allocation. This is especially important when dealing with large volumes of data and complex allocation formulas.
- Scenario Analysis: Automation facilitates scenario analysis. For example, companies can quickly assess the impact of changes in production volume or product mix on overhead costs and profitability.
Demonstrate how automation improves the accuracy of cost allocation
Automation improves the accuracy of cost allocation through several mechanisms, leading to more reliable cost information for decision-making. By reducing manual intervention and improving data integrity, automation minimizes errors and provides a more realistic view of costs.The ways automation enhances accuracy include:
- Reduced Human Error: Automated systems eliminate the potential for human errors in data entry, calculation, and allocation processes. This ensures that costs are allocated consistently and accurately, regardless of the volume of transactions.
- Enhanced Data Integrity: Automation integrates data from multiple sources, such as ERP systems, MES, and CRM systems, ensuring data consistency and completeness. This reduces the risk of inaccurate or missing data, which can distort cost allocations.
- Real-time Data Processing: Automation allows for real-time or near real-time data processing, providing up-to-date cost information. This is particularly important in dynamic environments where costs can change rapidly.
- Improved Data Validation: Automated systems can incorporate data validation rules to identify and correct errors before they impact cost allocations. For example, systems can flag unusual data entries or inconsistencies, ensuring that only valid data is used for allocation.
- More Sophisticated Allocation Methods: Automation enables the use of more sophisticated cost allocation methods, such as ABC, which provide a more detailed and accurate view of costs than traditional methods. This leads to a better understanding of cost drivers and more informed decision-making.
- Auditable Processes: Automated systems create an audit trail that tracks all data inputs, calculations, and allocation decisions. This improves transparency and allows for easy verification of cost allocations, which is crucial for regulatory compliance and internal controls.
Benefits of Automation in Cost Allocation
Automation significantly transforms cost allocation processes, bringing about substantial improvements in efficiency and accuracy. By leveraging technology, businesses can streamline their cost accounting practices, reducing manual effort and minimizing the potential for errors. This leads to more informed decision-making and improved financial management.
Efficiency and Time Savings
Automation drastically increases efficiency in cost allocation by eliminating manual tasks and accelerating data processing. The repetitive nature of cost allocation, which traditionally involves extensive manual data entry, calculations, and report generation, is ideally suited for automation. This shift not only speeds up the process but also frees up accounting staff to focus on more strategic activities.
- Reduced Processing Time: Automated systems can perform calculations and generate reports in a fraction of the time it takes manually. For example, a manufacturing company using automated cost allocation might process overhead costs for thousands of products within hours, compared to days or even weeks using manual methods.
- Faster Report Generation: Automation facilitates the rapid generation of various cost allocation reports, such as departmental cost summaries, product cost reports, and variance analyses. These reports can be produced on demand, providing timely insights for decision-making.
- Real-time Data Availability: With automated systems, cost allocation data is often updated in real-time, providing a continuous flow of information. This allows for quicker responses to changing cost structures and better financial control.
For instance, consider a retail chain with multiple stores. Before automation, calculating the cost of goods sold (COGS) for each store involved manually collecting sales data, inventory records, and other relevant information. This was a time-consuming process, often delaying the availability of accurate financial statements. Implementing automated systems, such as Enterprise Resource Planning (ERP) software, allows the chain to automatically allocate costs based on pre-defined rules, generating COGS calculations and store profitability reports in near real-time.
This provides store managers and the finance team with up-to-date financial information for strategic decision-making.
Impact on Reducing Human Error
Automation significantly minimizes the risk of human error in cost allocation. Manual processes are inherently prone to errors due to factors such as data entry mistakes, incorrect calculations, and misunderstandings of allocation methodologies. Automated systems, on the other hand, execute calculations based on pre-defined rules and algorithms, reducing the possibility of such errors.
- Elimination of Data Entry Errors: Automated data collection and processing systems reduce the need for manual data entry, thereby eliminating the risk of typos, transposition errors, and other inaccuracies.
- Consistent Application of Allocation Methods: Automation ensures that cost allocation methods are applied consistently across all cost objects. This consistency is critical for accurate reporting and comparison of costs over time.
- Reduced Calculation Errors: Automated systems perform calculations using pre-programmed formulas, minimizing the potential for arithmetic errors that can occur in manual calculations.
A common example of the impact of automation on reducing human error can be seen in the allocation of indirect costs in a manufacturing setting. Before automation, allocating overhead costs like rent, utilities, and depreciation involved manual calculations based on factors like machine hours or direct labor hours. This process was time-consuming and prone to errors. Automated systems can automatically track and allocate these costs based on pre-defined formulas, minimizing the risk of errors and ensuring consistent and accurate cost allocation.
For example, a manufacturing plant can use automated systems to track machine hours for each product and automatically allocate overhead costs based on these machine hours, eliminating the need for manual calculations and reducing the potential for errors.
Improvements in Accuracy
Automation directly enhances the accuracy of cost allocation by ensuring consistent data processing, eliminating human errors, and enabling the use of more sophisticated allocation methods. The result is more reliable cost information, which is essential for making informed business decisions.
- Accurate Data Collection: Automated systems integrate with other business systems, such as sales, inventory, and production, to automatically collect data. This integration ensures the data used for cost allocation is accurate and up-to-date.
- Precise Calculations: Automated systems perform calculations with precision, eliminating rounding errors and other inaccuracies that can occur in manual calculations.
- Enhanced Allocation Methodologies: Automation enables the use of more sophisticated allocation methods, such as activity-based costing (ABC), which provide a more accurate allocation of costs based on activities.
Consider a company that uses Activity-Based Costing (ABC) to allocate overhead costs. ABC involves identifying activities, determining the costs of those activities, and then allocating those costs to products or services based on their consumption of those activities. Implementing ABC manually can be complex and time-consuming. Automation simplifies this process. The automated system can track the activities, the resources consumed by each activity, and the cost drivers associated with each activity.
The system then automatically calculates the cost per activity and allocates the costs to the products or services based on their consumption of those activities. This automated approach provides a more accurate and detailed view of product costs compared to traditional allocation methods. For example, if a product consumes 20% of the machine setup activity, it will be allocated 20% of the cost associated with machine setups, providing a more precise cost allocation.
Automation and Real-time Costing
The integration of automation with cost allocation has paved the way for real-time costing, a significant advancement over traditional methods. This shift allows businesses to gain immediate insights into their costs, enabling more informed decision-making and improved operational efficiency. The ability to track and analyze costs as they occur provides a dynamic view of financial performance, empowering organizations to respond quickly to changes and opportunities.
Real-time Costing Enabled by Automation
Real-time costing, facilitated by automation, involves continuously tracking and allocating costs as they are incurred. This contrasts with traditional methods that often rely on periodic data collection and analysis, resulting in a delayed understanding of cost structures. Automation tools, such as Enterprise Resource Planning (ERP) systems and specialized cost accounting software, play a crucial role in enabling real-time costing. These systems automatically collect data from various sources, process it, and allocate costs based on pre-defined rules and algorithms.
Comparison of Traditional and Real-time Cost Allocation Approaches
Traditional cost allocation typically uses a periodic approach, often monthly or quarterly, to gather and analyze cost data. This involves manual data entry, spreadsheet-based calculations, and the application of predetermined overhead rates. In contrast, real-time cost allocation leverages automated systems to continuously collect, process, and allocate costs.Here’s a table summarizing the key differences:
Feature | Traditional Cost Allocation | Real-time Cost Allocation |
---|---|---|
Data Collection | Periodic, manual, and often time-consuming. | Continuous, automated, and integrated with various systems. |
Data Processing | Manual calculations, spreadsheet-based, and prone to errors. | Automated processing using algorithms and software. |
Allocation Frequency | Periodic (e.g., monthly, quarterly). | Continuous (e.g., daily, hourly, or even in real-time). |
Cost Visibility | Delayed and often retrospective. | Immediate and forward-looking. |
Decision-Making | Based on historical data, potentially leading to reactive decisions. | Supports proactive decision-making based on current cost information. |
Advantages of Real-time Cost Insights
Real-time cost insights provide several significant advantages for businesses. The ability to monitor costs as they occur allows for quicker identification of inefficiencies, improved resource allocation, and enhanced profitability.Key benefits include:
- Improved Decision-Making: Real-time data empowers managers to make more informed decisions based on the most current information. For example, a manufacturing company can immediately see the impact of a machine breakdown on production costs and take corrective action.
- Enhanced Cost Control: Continuous monitoring allows for proactive cost control measures. By identifying cost overruns in real-time, businesses can implement strategies to mitigate them before they escalate.
- Increased Efficiency: Real-time insights can reveal areas where processes can be streamlined and made more efficient. This could involve optimizing production schedules, reducing waste, or improving resource utilization.
- Better Pricing Strategies: Access to up-to-date cost data enables businesses to set more accurate prices for their products or services, ensuring profitability while remaining competitive.
- Faster Response to Market Changes: Real-time costing allows businesses to quickly adapt to changing market conditions. They can rapidly assess the cost implications of new product launches, changes in customer demand, or fluctuations in raw material prices.
Challenges of Implementing Real-time Cost Systems
Implementing real-time cost systems presents several challenges that organizations must address to ensure successful adoption. These challenges involve technological infrastructure, data integration, and organizational changes.Consider these challenges:
- System Integration: Integrating various data sources and systems, such as ERP, manufacturing execution systems (MES), and supply chain management systems, can be complex and require significant effort. Data must be seamlessly transferred and processed to provide real-time insights.
- Data Accuracy and Integrity: The accuracy and reliability of real-time cost data depend on the quality of the underlying data. Organizations must implement robust data validation processes to ensure that the information used for cost allocation is accurate and consistent.
- Technology Infrastructure: Implementing real-time cost systems often requires investments in new hardware and software, including high-performance databases and advanced analytics tools.
- Skill Gaps: Organizations may need to develop new skills or hire specialized personnel to manage and maintain real-time cost systems. This includes expertise in data analytics, cost accounting, and system administration.
- Organizational Change Management: Adopting real-time costing may require changes to existing processes, roles, and responsibilities. Effective change management is crucial to ensure that employees understand the benefits of the new system and are willing to adapt to the changes.
- Cost: The initial investment in technology, software, and training can be substantial. Organizations need to carefully evaluate the costs and benefits of implementing a real-time cost system.
Software and Tools for Automated Cost Allocation
The implementation of automated cost allocation necessitates the utilization of specialized software and tools designed to streamline the process. These solutions offer a range of features, from data collection and processing to the application of various allocation methods and reporting. Choosing the right software is crucial for maximizing efficiency and accuracy in cost management.
Comparing Different Cost Allocation Software
Several software options are available, each with its unique strengths and weaknesses. The choice depends on factors like company size, industry, and specific cost allocation needs. The following table provides a comparative overview of some popular cost allocation software, focusing on key features and capabilities.
Software | Key Features | Integration Capabilities | Target Users |
---|---|---|---|
SAP S/4HANA | Comprehensive cost accounting, real-time data processing, advanced allocation methods (e.g., activity-based costing), robust reporting and analytics. | Seamless integration with other SAP modules (e.g., FI, CO, MM, SD), third-party systems via APIs and connectors. | Large enterprises with complex operations and extensive IT infrastructure. |
Oracle NetSuite | Cloud-based solution, automated cost allocation, flexible reporting, multi-currency support, budgeting and forecasting tools. | Integration with other NetSuite modules, third-party applications via APIs. | Mid-sized to large businesses seeking a cloud-based, integrated solution. |
Vena Solutions | Budgeting, planning, and forecasting, cost allocation functionality, data visualization, integration with Excel. | Integration with various ERP and financial systems through connectors and APIs, Microsoft Excel integration. | Businesses seeking robust budgeting and planning capabilities alongside cost allocation. |
Host Analytics (Workday Adaptive Planning) | Cloud-based planning and analytics, cost allocation features, scenario planning, reporting and dashboards. | Integration with Workday Financial Management, other ERP and financial systems. | Businesses focused on planning and analysis, seeking a cloud-based solution. |
Features Offered by Leading Automation Tools
Automation tools provide a rich set of features designed to simplify and improve cost allocation processes. Understanding these features helps in selecting the right tool for a company’s needs.
- Automated Data Import and Preparation: Automated import of data from various sources (e.g., ERP systems, spreadsheets) and data cleansing capabilities. This minimizes manual data entry and reduces errors.
- Flexible Allocation Methods: Support for various allocation methods, including direct, step-down, reciprocal, and activity-based costing (ABC). Users can select and customize allocation methods based on their specific requirements.
- Rule-Based Allocation Engine: Allows users to define allocation rules based on predefined criteria (e.g., headcount, square footage, machine hours). The system automatically applies these rules to allocate costs.
- Real-Time Reporting and Analytics: Provides real-time visibility into cost allocation results through dashboards, reports, and visualizations. This enables timely decision-making and performance monitoring.
- Audit Trail and Compliance: Maintains a complete audit trail of all allocation activities, ensuring transparency and compliance with regulatory requirements.
- Integration Capabilities: Seamless integration with existing financial systems, ERP systems, and other business applications. This eliminates data silos and ensures data consistency.
- User-Friendly Interface: Intuitive user interface with drag-and-drop functionality and customizable dashboards.
- Scenario Planning: Ability to model different allocation scenarios to assess the impact of various decisions on cost allocation.
Examples of System Integration
Integration capabilities are critical for automated cost allocation tools. They allow the seamless flow of data between different systems, reducing manual effort and improving data accuracy.
- Integration with ERP Systems: A cost allocation tool integrates with an ERP system (e.g., SAP, Oracle, Microsoft Dynamics 365) to import cost data (e.g., labor, materials, overhead) and allocate them based on predefined rules. For instance, the system can pull labor hours from the ERP system’s time tracking module and allocate labor costs to specific projects or departments.
- Integration with Financial Reporting Systems: The tool integrates with financial reporting systems to automatically post allocated costs to the general ledger. This ensures that cost allocation results are reflected in financial statements. For example, after allocating overhead costs, the system automatically creates journal entries in the general ledger to reflect the allocation.
- Integration with Data Warehouses: The tool integrates with data warehouses (e.g., Snowflake, Amazon Redshift) to store and analyze large volumes of cost data. This enables advanced reporting and analytics. For instance, historical cost data can be analyzed to identify cost drivers and trends, allowing for more informed allocation decisions.
- Integration with Budgeting and Planning Tools: The tool integrates with budgeting and planning tools to incorporate allocated costs into budgets and forecasts. This allows for more accurate financial planning. For example, allocated costs can be included in departmental budgets to provide a comprehensive view of expenses.
Demonstrating the User Interface of a Cost Allocation Automation Tool
The user interface (UI) of a cost allocation tool is crucial for its usability and effectiveness. A well-designed UI simplifies the process of setting up, managing, and analyzing cost allocations.
Imagine a screenshot of a hypothetical cost allocation tool’s UI. The interface is clean and intuitive, with a clear layout. The main screen is divided into several sections.
On the left side is a navigation pane with options such as “Data Import,” “Allocation Rules,” “Reports,” and “Settings.” The “Data Import” section allows users to upload data from various sources, such as CSV files or direct connections to ERP systems. In the “Allocation Rules” section, users can define allocation methods and criteria. For example, a user might set up an allocation rule to allocate rent based on square footage, specifying the building’s total square footage and the square footage occupied by each department.
The “Reports” section provides a variety of pre-built and customizable reports, including allocation summaries, cost breakdowns, and variance analysis. The “Settings” section allows users to configure system settings, manage users, and define security roles.
The central part of the screen displays a dashboard showing key performance indicators (KPIs) related to cost allocation, such as total allocated costs, allocation variances, and cost per unit. These KPIs are presented through interactive charts and graphs, enabling users to quickly identify trends and anomalies. For example, a pie chart illustrates the distribution of allocated overhead costs across different departments.
Below the dashboard, a detailed table displays the results of the latest cost allocation run, showing the allocated costs for each cost object, along with the allocation basis and allocation percentage.
At the top of the screen, a menu bar provides quick access to frequently used functions, such as saving, exporting reports, and accessing help documentation. The UI includes features like drag-and-drop functionality for defining allocation rules, interactive data visualizations, and customizable dashboards, making the process of cost allocation more efficient and user-friendly. The UI design emphasizes clarity, ease of use, and the ability to quickly access and understand critical cost allocation information.
Impact of Automation on Cost Allocation in Different Industries
Automation’s influence on cost allocation varies significantly across industries, reflecting the diverse operational models and data requirements. The adoption of automated systems streamlines processes, enhances accuracy, and provides more granular insights into cost drivers. This section explores the specific applications and impacts of automation in manufacturing, service, healthcare, and financial services.
Manufacturing Cost Allocation
Manufacturing industries heavily rely on accurate cost allocation to determine product pricing, profitability, and efficiency. Automation plays a crucial role in streamlining this process.In manufacturing cost allocation, automation can:
- Automate data collection from various sources, including shop floor systems, sensors, and ERP systems, to capture labor hours, machine usage, and material consumption.
- Implement activity-based costing (ABC) systems, where automated systems track activities and their associated costs, such as machine setups, inspections, and material handling.
- Facilitate the allocation of overhead costs, like utilities and rent, based on automated calculations using pre-defined allocation bases (e.g., machine hours, direct labor hours).
- Generate real-time cost reports and dashboards, enabling timely decision-making and performance monitoring.
For instance, a factory producing electronic components can use automated systems to track the energy consumption of each machine involved in the production process. This data, integrated with machine-hour information, allows for precise allocation of energy costs to individual products, leading to accurate product costing and better pricing strategies. Another example involves automated tracking of raw material usage through sensors and ERP integration, which facilitates precise allocation of material costs to specific products or production batches.
Service Industry Cost Allocation
The service sector, with its emphasis on labor, indirect costs, and diverse service offerings, benefits significantly from automated cost allocation. Automation helps service providers optimize resource allocation and enhance profitability.Automation in the service industry can be employed in the following ways:
- Automating time tracking for employees and projects, ensuring accurate allocation of labor costs to specific services or projects.
- Utilizing automated systems to track and allocate indirect costs, such as office rent, utilities, and administrative expenses, based on pre-defined allocation bases (e.g., square footage, number of employees).
- Implementing automated billing and invoicing systems, streamlining the process of charging clients for services rendered and providing detailed cost breakdowns.
- Leveraging data analytics and reporting tools to identify cost drivers and optimize resource allocation.
For example, a consulting firm can use automated time-tracking software integrated with project management systems. This enables the firm to allocate labor costs to specific projects based on the actual hours worked by consultants. This data can then be used to calculate project profitability and inform pricing decisions for future projects. Similarly, a marketing agency can automate the allocation of overhead costs (e.g., office rent, software licenses) based on the number of clients served or the revenue generated by each client.
Healthcare Sector Automation
The healthcare sector faces unique cost allocation challenges, including complex billing processes, regulatory requirements, and the need for accurate cost information for patient care and financial management. Automation is becoming increasingly vital in this sector.Automation’s role in healthcare includes:
- Automating the collection and processing of patient data, including medical records, treatment details, and insurance information, to accurately allocate costs to specific procedures and patients.
- Implementing automated billing and coding systems to ensure accurate and timely claims submission and revenue recognition.
- Utilizing activity-based costing (ABC) to allocate costs to specific activities, such as surgeries, diagnostic tests, and patient consultations, enabling a better understanding of the cost of providing care.
- Generating real-time dashboards and reports to monitor costs, identify inefficiencies, and support decision-making.
For instance, hospitals can use automated systems to track the utilization of medical equipment and supplies for each patient. This data, combined with labor costs and other expenses, allows for the accurate allocation of costs to individual patients and procedures. Automated systems also help in generating detailed cost reports for different departments and services, enabling hospital administrators to identify areas for cost reduction and efficiency improvements.
For example, a hospital could automate the allocation of pharmaceutical costs based on patient medication records and dosage information, ensuring accurate cost assignment to each patient’s treatment plan.
Financial Services Cost Allocation
Financial services firms, including banks, insurance companies, and investment firms, require sophisticated cost allocation systems to manage costs, assess profitability, and comply with regulatory requirements. Automation plays a critical role in these firms.Automation’s impact on financial services includes:
- Automating the allocation of costs across various business units, products, and services, based on pre-defined allocation bases (e.g., transaction volume, assets under management).
- Implementing sophisticated ABC systems to allocate costs to specific activities, such as customer service, loan processing, and investment management.
- Automating the generation of regulatory reports and financial statements, ensuring compliance with industry regulations.
- Utilizing data analytics and reporting tools to analyze cost drivers, identify inefficiencies, and support strategic decision-making.
For example, a bank can use automated systems to allocate the costs of its branch network based on factors like customer transactions, the number of accounts, and the square footage of each branch. This data helps the bank assess the profitability of each branch and make informed decisions about branch operations and resource allocation. Similarly, an insurance company can automate the allocation of overhead costs, such as IT infrastructure and marketing expenses, to different insurance products based on factors like policy volume and premium revenue.
This allows the company to assess the profitability of each product line and make informed pricing and marketing decisions.
Challenges and Considerations in Automating Cost Allocation
Automating cost allocation, while offering numerous advantages, presents several challenges that organizations must carefully consider before implementation. These challenges range from upfront investment costs to ongoing maintenance and the need for workforce adaptation. A thorough understanding of these factors is crucial for a successful and sustainable automation strategy.
Initial Investment Costs Associated with Automation
The initial investment in automating cost allocation can be substantial, encompassing various elements that contribute to the overall expense. These costs must be carefully evaluated to determine the feasibility and return on investment of the automation project.
- Software Licensing and Implementation: The acquisition of specialized software is often the most significant initial cost. This includes the purchase of licenses for cost allocation software, enterprise resource planning (ERP) systems with cost accounting modules, or custom-developed solutions. Implementation costs can vary significantly depending on the complexity of the system and the extent of customization required. For example, a large multinational corporation might spend hundreds of thousands or even millions of dollars on a comprehensive ERP system implementation, while a small business might opt for a more affordable cloud-based solution.
- Hardware Infrastructure: Depending on the chosen solution, additional hardware might be necessary. This could include servers, storage devices, and network upgrades to support the software and handle the increased data processing demands. Cloud-based solutions, however, can mitigate the need for significant hardware investments.
- Consulting and Integration Services: Organizations often require the expertise of consultants and system integrators to assist with software selection, configuration, data migration, and integration with existing systems. These services can add considerable expense to the initial investment.
- Data Migration and Cleansing: Transferring existing cost data into the new automated system can be a complex and time-consuming process. This often involves data cleansing to ensure accuracy and consistency, which may require dedicated resources and specialized tools.
- Training: Adequate training for employees on the new system is crucial for successful adoption and utilization. Training programs can incur costs associated with instructor fees, training materials, and employee time spent in training sessions.
Implementation Complexities of Different Automation Solutions
The complexity of implementing an automated cost allocation system varies considerably depending on the chosen solution and the organization’s specific requirements. The selection of the right approach requires a careful evaluation of several factors.
- Complexity of Existing Cost Allocation Methods: Organizations with highly complex cost allocation methods, involving numerous cost pools, allocation bases, and intricate calculations, will typically face more complex implementation challenges. For example, a manufacturing company with multiple production processes and a wide range of overhead costs will likely require a more sophisticated solution compared to a service-based business with simpler cost structures.
- Integration with Existing Systems: The seamless integration of the automated cost allocation system with other existing systems, such as ERP, financial reporting, and operational databases, is critical. Complex integrations can require significant customization and testing, adding to the implementation effort.
- Data Volume and Quality: Organizations that handle large volumes of data and/or have data quality issues will face increased implementation complexity. Data cleansing, validation, and transformation become more critical and time-consuming in such scenarios.
- Customization Requirements: The need for customization, whether to tailor the software to specific business processes or to integrate with unique systems, can significantly increase implementation complexity. Custom development often involves more extensive testing and ongoing maintenance.
- Vendor Expertise and Support: The experience and expertise of the software vendor and implementation partners can greatly impact the success and ease of implementation. Choosing a vendor with a proven track record and strong support capabilities is crucial.
Potential Data Security Concerns
Automating cost allocation involves handling sensitive financial data, making data security a paramount concern. Implementing robust security measures is essential to protect against data breaches, unauthorized access, and other security threats.
- Data Encryption: Implementing encryption for data both in transit and at rest is a fundamental security measure. This protects data from unauthorized access, even if the system is compromised.
- Access Controls and User Permissions: Implementing strict access controls and user permissions ensures that only authorized personnel can access sensitive data. Role-based access control (RBAC) is a common approach, where users are granted access based on their job roles and responsibilities.
- Regular Security Audits and Vulnerability Assessments: Conducting regular security audits and vulnerability assessments helps identify and address potential security weaknesses. This includes penetration testing and other security testing methods.
- Data Backup and Disaster Recovery: Implementing a comprehensive data backup and disaster recovery plan is crucial to ensure data availability in case of a system failure or disaster. This includes regular backups, offsite storage, and procedures for restoring data.
- Compliance with Data Privacy Regulations: Organizations must comply with relevant data privacy regulations, such as GDPR, CCPA, and others. This includes obtaining consent for data collection, providing data subject rights, and implementing appropriate security measures to protect personal data.
Need for Employee Training
Successfully implementing and utilizing an automated cost allocation system requires adequate employee training. Training ensures that employees understand the new system, can effectively use its features, and can adapt to the changes in their roles and responsibilities.
- Understanding the New System: Training should cover the functionalities of the automated system, including data entry, report generation, and system navigation. Employees need to understand how the system works and how it impacts their daily tasks.
- Changes in Roles and Responsibilities: Automation can lead to changes in job roles and responsibilities. Training should address these changes, helping employees understand their new roles and how they contribute to the overall cost allocation process.
- Data Analysis and Interpretation: Employees should be trained on how to analyze and interpret the data generated by the automated system. This includes understanding key performance indicators (KPIs), identifying trends, and using the data to make informed decisions.
- Troubleshooting and Problem Solving: Training should equip employees with the skills to troubleshoot common issues and resolve problems that may arise. This includes providing access to support resources and documentation.
- Ongoing Training and Development: The need for training does not end with the initial implementation. Ongoing training and development are essential to keep employees updated on new features, system updates, and best practices. This can include refresher courses, webinars, and access to online learning resources.
Role of Automation in Budgeting and Forecasting
Automation significantly transforms budgeting and forecasting processes, enabling organizations to create more accurate, efficient, and responsive financial plans. By automating repetitive tasks, integrating data sources, and leveraging advanced analytics, businesses can improve decision-making and adapt more effectively to changing market conditions. This leads to improved financial performance and strategic agility.
Automation and Budgeting: A Comparative Table
Automation streamlines the budgeting process, offering several advantages over traditional manual methods. The following table highlights the key differences.
Manual Budgeting | Automated Budgeting | Impact | Benefits |
---|---|---|---|
Time-consuming data collection and entry. | Automated data extraction from various sources (ERP, CRM, etc.). | Significant reduction in time spent on data entry. | Faster budget cycles, freeing up resources for analysis. |
Prone to human error in calculations and data manipulation. | Automated calculations and error checks. | Improved data accuracy and reduced errors. | More reliable budget forecasts. |
Limited ability to perform “what-if” scenarios. | Automated scenario planning and sensitivity analysis. | Enhanced ability to model different scenarios. | Better informed decision-making based on various potential outcomes. |
Difficult to track budget variances in real-time. | Automated variance analysis and real-time reporting. | Faster identification of variances and potential issues. | Proactive adjustments to maintain financial goals. |
Steps for Using Automation in Cost Forecasting
Implementing automation in cost forecasting involves a structured approach to ensure effective results. The process typically includes these steps:
- Data Integration: Consolidate data from diverse sources, such as accounting systems, sales records, and operational databases. This ensures a comprehensive and unified data foundation.
- Data Cleaning and Preparation: Standardize and clean the data to eliminate errors and inconsistencies. This includes handling missing values, correcting inaccuracies, and ensuring data compatibility for analysis.
- Model Selection and Development: Choose the appropriate forecasting model based on the nature of the data and business requirements. Examples include time series analysis, regression models, and machine learning algorithms. Develop and train these models using the prepared data.
- Automation Implementation: Automate the forecasting process using software tools or programming languages. This involves scheduling data updates, model execution, and report generation.
- Performance Monitoring and Refinement: Continuously monitor the performance of the forecasting models. Regularly evaluate forecast accuracy and refine models as needed. This ensures the models remain relevant and reliable over time.
Examples of Enhanced Budgeting Accuracy Through Automation
Automation enhances budgeting accuracy through several mechanisms, resulting in more precise financial forecasts. These improvements are critical for effective financial planning.
- Automated Data Aggregation: Imagine a retail company with multiple stores. Instead of manually collecting sales data from each store, automation can pull this information directly from point-of-sale systems, streamlining the process and reducing errors. This leads to more accurate sales forecasts.
- Scenario Planning: Consider a manufacturing firm. Automation can quickly generate different budget scenarios based on changes in raw material costs, labor rates, and demand. This capability helps the company prepare for various economic conditions.
- Real-time Budget Updates: A software company can integrate its budgeting system with its project management software. As project costs are incurred, the budget is updated in real-time, providing a current view of project profitability.
- Variance Analysis: A healthcare provider can automate the analysis of variances between budgeted and actual expenses. This allows for prompt identification of cost overruns or savings, facilitating timely corrective actions.
Impact of Automation on Variance Analysis
Automation revolutionizes variance analysis, providing several benefits. This allows for faster, more detailed, and insightful financial analysis.
- Faster Identification of Variances: Automation enables real-time comparison of actual versus budgeted figures, accelerating the identification of variances. This contrasts with manual processes that often involve delays.
- Improved Accuracy: Automated calculations minimize human error, ensuring more reliable variance analysis results. This contrasts with manual calculations that can be prone to mistakes.
- Deeper Insights: Automation facilitates deeper dives into the causes of variances. For example, it can analyze sales volume, pricing changes, and cost fluctuations.
- Enhanced Reporting: Automated systems generate detailed variance reports, including visual aids, which aid in conveying complex financial information.
- Proactive Decision-Making: By providing timely and accurate variance analysis, automation enables proactive decision-making. For example, managers can take immediate action to address unfavorable variances or capitalize on favorable ones.
Future Trends in Automation and Cost Allocation
The evolution of automation in cost allocation is accelerating, driven by advancements in technologies like artificial intelligence, machine learning, and blockchain. These innovations promise to revolutionize how businesses manage and analyze costs, leading to greater efficiency, accuracy, and strategic decision-making. The future of cost allocation will be characterized by increased sophistication and integration, transforming traditional practices.
Role of Artificial Intelligence (AI) in Cost Allocation
AI is poised to significantly impact cost allocation by enabling more intelligent and adaptive processes. AI algorithms can analyze vast datasets, identify patterns, and make predictions with a level of accuracy and speed previously unattainable. This leads to improved cost visibility and control.AI’s capabilities in cost allocation include:
- Predictive Analytics: AI can forecast future costs based on historical data, market trends, and other relevant factors. For example, AI could analyze sales data, production schedules, and raw material prices to predict the cost of goods sold with greater precision.
- Anomaly Detection: AI algorithms can identify unusual spending patterns or discrepancies in cost data, alerting businesses to potential issues like fraud or inefficiencies. For instance, AI could flag unusually high maintenance costs for a specific machine or unexpected increases in labor expenses.
- Automated Allocation: AI can automate the allocation of costs based on predefined rules and complex algorithms. This minimizes manual intervention and reduces the risk of human error.
- Optimization of Allocation Methods: AI can analyze the effectiveness of different cost allocation methods and recommend the most appropriate approach for specific situations.
How Machine Learning Can Optimize Cost Allocation
Machine learning, a subset of AI, offers powerful tools for optimizing cost allocation processes. Machine learning algorithms can learn from data, adapt to changing conditions, and continuously improve their performance. This leads to more accurate and efficient cost allocation.Machine learning techniques applied to cost allocation include:
- Clustering: Machine learning algorithms can group similar cost items together, making it easier to allocate costs to the appropriate cost objects. For example, clustering could group similar product lines or customer segments for more accurate cost assignment.
- Classification: Machine learning can classify costs into different categories, such as direct materials, direct labor, and overhead. This improves cost tracking and analysis.
- Regression Analysis: Machine learning can be used to model the relationship between costs and cost drivers, enabling more accurate cost allocation. For example, regression analysis can help determine the relationship between machine hours and overhead costs.
- Recommendation Systems: Machine learning can suggest the most appropriate cost allocation methods based on the specific characteristics of a business and its cost structure.
Potential of Blockchain Technology in this Area
Blockchain technology, known for its secure and transparent nature, holds significant potential for revolutionizing cost allocation. By creating immutable records of transactions and costs, blockchain can enhance the accuracy, auditability, and transparency of cost allocation processes.The benefits of blockchain in cost allocation include:
- Enhanced Data Integrity: Blockchain’s decentralized and immutable nature ensures that cost data cannot be altered or tampered with, providing a high level of data integrity.
- Improved Auditability: All cost allocation transactions are recorded on the blockchain, creating a complete and transparent audit trail. This simplifies the auditing process and reduces the risk of fraud.
- Increased Transparency: Blockchain allows stakeholders to view cost allocation data in real-time, increasing transparency and trust.
- Streamlined Processes: Blockchain can automate and streamline cost allocation processes, reducing the need for manual intervention and paperwork.
Emerging Trends Shaping the Future of Automated Cost Allocation
Several emerging trends are influencing the future of automated cost allocation, leading to more sophisticated and integrated solutions. These trends are expected to drive significant changes in the way businesses manage and analyze costs.Key trends include:
- Integration with Enterprise Resource Planning (ERP) Systems: Automated cost allocation tools are increasingly being integrated with ERP systems to provide a seamless flow of data and improve the efficiency of cost management processes.
- Cloud-Based Solutions: Cloud-based cost allocation software is gaining popularity due to its scalability, flexibility, and accessibility.
- Real-Time Costing: The shift towards real-time costing, enabled by automation, allows businesses to monitor costs continuously and make more informed decisions.
- Focus on Sustainability: Businesses are increasingly focusing on incorporating sustainability considerations into cost allocation, such as allocating costs based on environmental impact.
- Rise of Hyperautomation: Hyperautomation, which combines AI, machine learning, and robotic process automation (RPA), is being used to automate complex cost allocation processes end-to-end.
Case Studies of Successful Automation Implementation
The implementation of automation in cost allocation has yielded significant benefits for various organizations, leading to improved efficiency, accuracy, and insights. Analyzing real-world case studies provides valuable lessons and demonstrates the practical application of these technologies. These examples showcase how automation can transform cost allocation processes and contribute to better decision-making.
Case Study: Manufacturing Company’s Activity-Based Costing (ABC) Implementation
A medium-sized manufacturing company, producing customized industrial equipment, faced challenges in accurately allocating overhead costs using a traditional, volume-based method. This resulted in inaccurate product costing and hindered profitability analysis. The company decided to implement an automated ABC system to improve cost allocation accuracy and gain better insights into its operations.To successfully implement the automated ABC system, the following key steps were taken:
- Process Mapping: The company meticulously mapped its key manufacturing processes, identifying all activities and cost drivers. This involved detailed analysis of each stage of production, from raw material procurement to final product delivery.
- Data Collection and Integration: An automated data collection system was established, integrating data from various sources, including the Enterprise Resource Planning (ERP) system, shop floor data collection systems, and other relevant databases. This centralized data collection streamlined the process and minimized manual data entry errors.
- Cost Driver Identification: The company identified and selected appropriate cost drivers for each activity. This involved analyzing the relationship between activities and their associated costs, ensuring the drivers accurately reflected resource consumption. For example, machine hours were identified as a cost driver for machine maintenance costs.
- Software Implementation and Configuration: A specialized cost allocation software was selected and implemented. The software was configured to align with the company’s identified activities, cost drivers, and cost pools.
- Training and User Adoption: Employees were trained on the new system and the principles of ABC. This ensured they understood how to use the software and interpret the results effectively.
The automation of the ABC system delivered several quantifiable benefits:
- Improved Product Costing Accuracy: The company observed a 15% improvement in the accuracy of product costing, leading to more informed pricing decisions.
- Enhanced Profitability Analysis: The automated system provided detailed insights into the profitability of individual products and product lines, enabling the company to identify and address underperforming areas.
- Reduced Overhead Cost Allocation Time: The time required to allocate overhead costs was reduced by 60%, freeing up accounting staff for other value-added activities.
- Better Resource Allocation: The company was able to identify and eliminate inefficient processes, leading to improved resource allocation and reduced operational costs.
The manufacturing company’s successful implementation of automated ABC revealed valuable lessons:
“Careful planning, data integration, and employee training are crucial for a successful automation implementation. Selecting the right software and accurately identifying cost drivers are also key factors.”
The case study highlights the importance of selecting appropriate cost drivers. Using machine hours as a cost driver for machine maintenance costs provides a clear example of a direct correlation.
Final Thoughts
In summary, automation is no longer a futuristic concept but a present-day necessity for effective cost allocation. By embracing automated systems, businesses can achieve greater efficiency, accuracy, and real-time visibility into their financial operations. As technology continues to advance, the role of automation in cost allocation will only become more pronounced, offering new opportunities for optimization and strategic advantage. The future of cost management is undoubtedly automated, promising a more insightful and data-driven approach to financial decision-making.
Answers to Common Questions
What are the primary benefits of automating cost allocation?
The primary benefits include increased efficiency, reduced human error, improved accuracy, and real-time visibility into costs, leading to better decision-making and cost optimization.
How does automation improve the accuracy of cost allocation?
Automation reduces manual data entry errors, ensures consistent application of allocation methods, and allows for more frequent data updates, leading to more precise cost assignments.
What types of businesses can benefit from automated cost allocation?
Businesses of all sizes and across various industries, including manufacturing, service, healthcare, and financial services, can benefit from automated cost allocation.
What are the initial investment costs associated with automation?
Initial investment costs can include software licensing fees, implementation costs, and employee training expenses. However, these costs are often offset by long-term savings and improved efficiency.